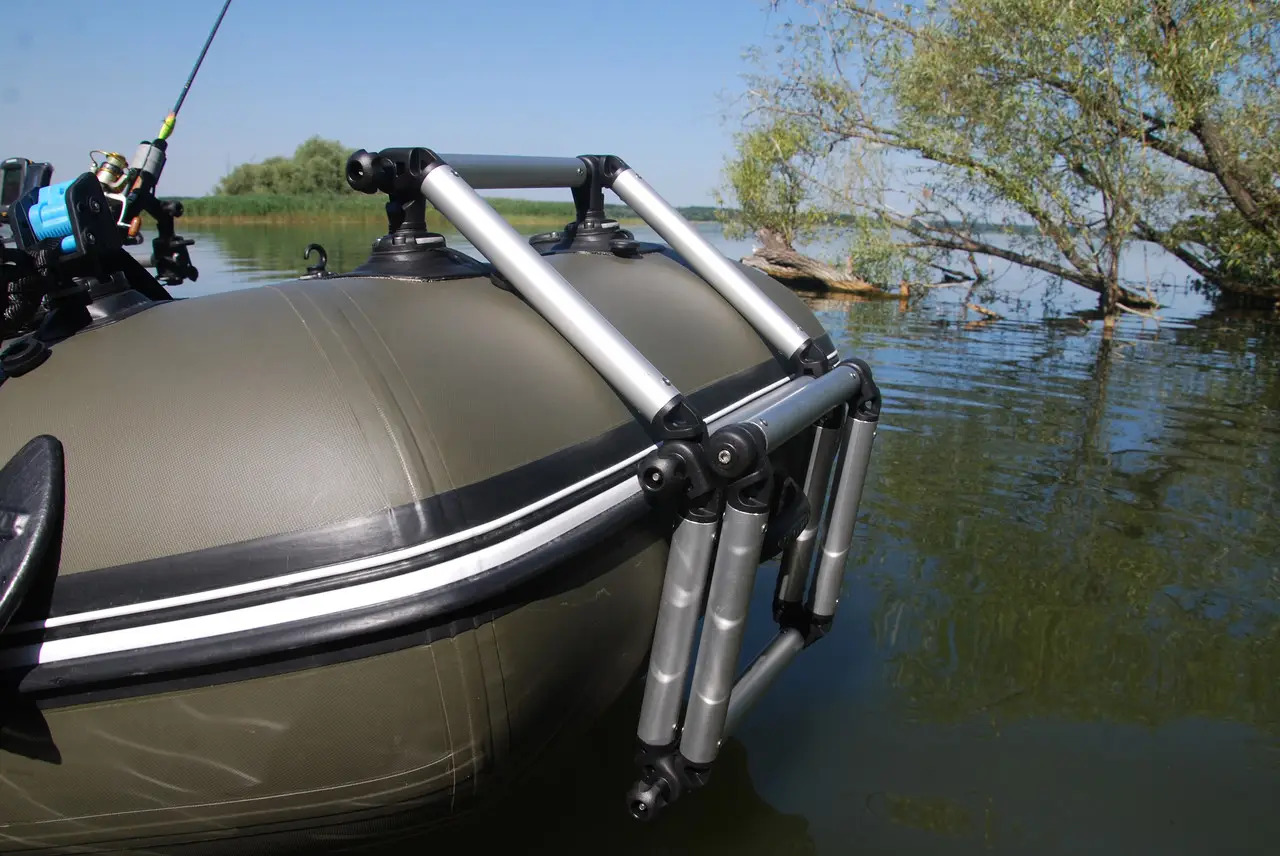
The seams on inflatable boats differ both in terms of execution technology (welded, glued, or combined) and sealing method (single-sided, also known as external, classic, and reinforced).
Welded seams have an advantage over glued ones; they are much stronger, not susceptible to delamination when heated, etc. However, they have a drawback: during the welding process, the fabric is exposed to high temperatures (around 600 degrees) and grooves of weakened material appear along the edge of the tape. If you closely inspect such a seam, you'll notice a small groove along the edge of the tape. This area experienced fabric heating, but the width of the tape isn't always sufficient to close it.
Glued seams look nice but are very temperamental and unreliable. The adhesive used for assembling the boat has temperature activation, and the slightest errors or deviations from the adhesive storage method and assembly process can cause the boat to come apart at the seams when exposed to sunlight.
For this reason, serious manufacturers tend to lean towards combined seams. The boat is assembled using welding, and then the welded seams are reinforced with adhesive tapes. This way, the seams become both strong and aesthetically pleasing.
Now that we've covered the technology, let's delve into the sealing method.
We won't consider single-sided seams; this is the cheapest and least reliable way of assembling a boat. Regardless of whether it's a welded or glued seam, such a boat won't last long and could even be dangerous. Such a boat isn't suitable for navigation and can only be used as a toy in shallow waters. Some Chinese and Russian manufacturers employ this method.
Classic seam: the most commonly used seam for boat assembly. It is strong enough and, with a combined technology, very durable. However, it has a few drawbacks: the upper protective tape is applied to the inflated boat, and like any glued seam, it is susceptible to sun-induced issues, as the tape is directly adhered to the joint of two boat parts. It can "bubble" or develop wrinkles due to heat. Imagine two parts joined by a flexible tape and how they behave when shifting against each other. With proper assembly, this won't cause any issues, but the appearance of the boat might be slightly compromised.
Hence, the most reliable choice is the reinforced seam. European manufacturers like 'ZODIAC,' 'RAPTOR,' 'IBOAT,' American 'MERCURY,' and Japanese 'HONDA' (yes, 'HONDA' produces not only motors, motorcycles, and cars but also inflatable boats) employ this method. It's practically the same as the classic seam, but it features a technological tape made of special PVC. This tape is different from the external and internal tapes; it's more elastic and durable, and it firmly bonds the boat parts during welding. However, since it has weakened edges due to the welding process (which we discussed when looking at assembly technology), it needs to be covered with decorative adhesive tape. Such a seam will be everlasting, resistant to shifting or delamination. It's both durable and visually appealing.